UV debonding machine optical lens, LED, IC, semiconductor, integrated circuit board, mobile hard disk and other semiconductor materials UV film degumming use
Paramerters :
Type | DSX-UV350L | Outside Dimension | 453*553*500mm |
Power | 2400W | Emitted Area | 350*350mm |
Voltage | 58V | Irradiation Height | 50mm |
Current | 40A | Curing Speed | 1-10s |
Service Life | 20000 hours | Control | PLC |
Cooling Method | Air Cooling | Input Voltage | 220V |
Control Method | PLC automatic control | Weight | 76.5kg |
Screen Size | 7 inch | Standby Power | 90W |
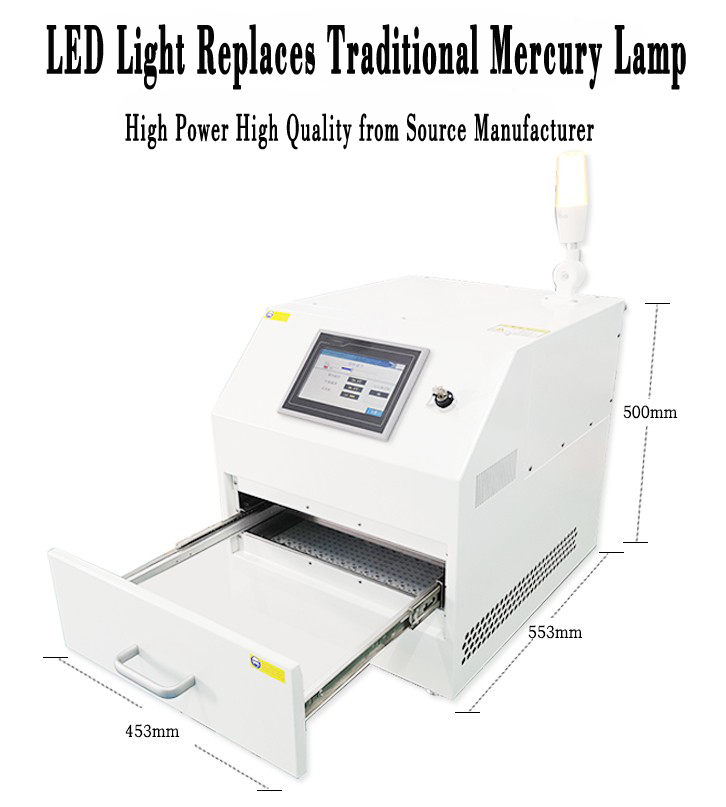
UV Dissolver Performance and Features:
The curing speed of the adhesive is generally 30-40 seconds, but depending on the adhesive properties and suitability of the film and the wavelength of the lamp, the curing time will increase or decrease, but this system It is highly applicable. For example, it can be used in R&D and a large variety of production lines for UV film debonding of semiconductor materials such as optical lenses, LEDs, ICs, semiconductors, integrated circuit boards, and mobile hard disks.
Introduction :
UV debonding machine is suitable for 6/8/12’’ chip whole chip irradiation use, the theme part is made of stainless steel, aluminum alloy, reliable refrigeration, stable performance, high film precision and stability, simple operation.
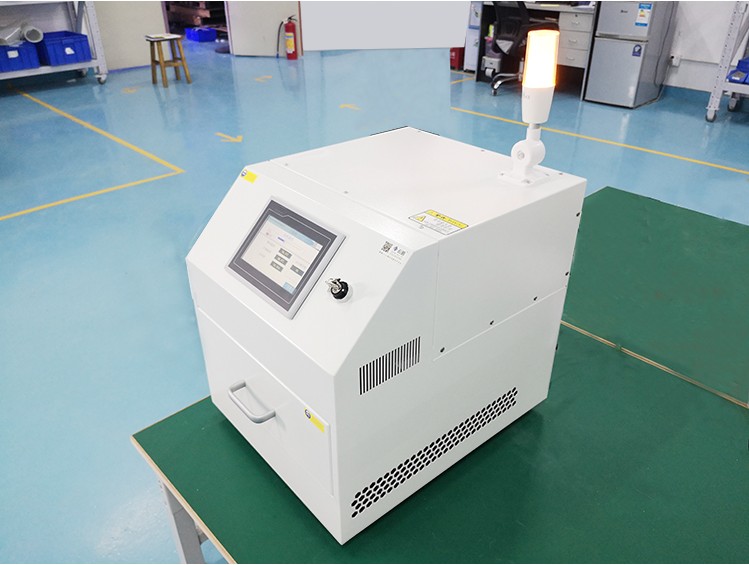

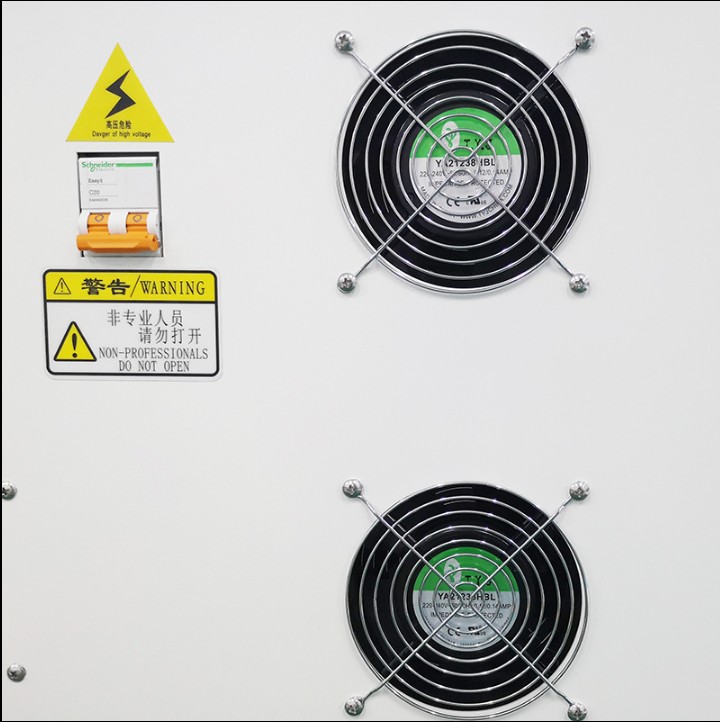
What are Features of UV Dissolver Features?
1. Wafer size: up to 6 inch, 8 inch, 12 inch
2. The operator simply places/unloads the work, and the other work is fully automatic.
3. So small, the desktop model contains imported cold light source to uniformly produce light with a wavelength of 350-400nm, eliminating the glue of the film.
4, with low temperature, uniform exposure, compact structure, low energy consumption, is the ideal model for the semiconductor industry
Reading
In the ordinary dispenser manufacturers, such as some dispensing controllers, the domestic imitation technology is very mature, the market competition is very fierce, the price has plummeted, and even a few machines have appeared. However, domestic dispensers generally have low precision and are not stable enough. Some high-tech industries, when it comes to purchasing glue dispensers, can only find world brands.Therefore, in the case of high precision, it is waiting for the people with lofty ideals to make further efforts.When the market is fiercely competitive, only quality and service can make you stand out.
How to Process the Dispenser?
1. Opening the glue
when opening the rubber head, because there is a gap between the rubber outlet and the rubber valve, there is no glue between the rubber nozzles. If the rubber outlet is opened, the movement will start immediately. Lead to a short section of lack of glue at the beginning of the track. In order to avoid this situation, after the glue is opened, it is postponed for a while, waiting for the glue to flow out, and then perform the subsequent movement. This delay time is called the glue opening delay.
2. After the rubber is
closed, there is still no glue flowing between the rubber outlet and the rubber valve. If it is moved immediately after closing the rubber head, it may constitute a glue tailing phenomenon. In order to avoid the attack, after the rubber head is closed, the glue is allowed to flow for a while, and then the follow-up action is performed.This delay is called the glue delay.
3. The height of the drawing is high
because the viscosity of some glues is large, and the gap is slowly raised at a constant speed to break the glue, which does not affect the glue track. This interval is called the drawing height.
4. Lifting Height
When the track is finished, after moving to the starting point of the next track, in order to avoid the impact of the rubber head, lift the rubber head up to a height at the finished point to ensure that the rubber head is safe to hit the needle, and then move to the next section. The starting point of the track, this height is called the lifting height.
5. Early closing of the glue
to close the glue, that is, the early closing of the glue interval means that in the continuous track coating, the plastic head is closed before reaching the end point, and the residual pressure and the excess glue are used to finish the final section of the track to avoid the pile of glue. i.e., the length of this track "glue off interval." complete action
After the dispensing of the entire teaching track is completed, in order to facilitate the pick-and-place of the workpiece, increase the processing power or eliminate the processing error, the user can set the glue head to move to the specified orientation, or the starting point of the processing file, or the processing file completion point, or reset, or File connection. This project is called the completion action.
6. Pulling up and Lifting
because of the viscosity of the glue, the wire drawing action after the glue is closed can not reach the action of pulling the broken wire, and the shape of the pulled rubber wire may not meet the requirements. Therefore, after closing the rubber head, performing the diagonal pull up action for the wire drawing preparation
7. Glue Heating
can try to heat the glue to a suitable temperature, the fluidity of the added glue, and can also handle the drawing in a certain sense! Keep an eye on the temperature of the heating is not too high!
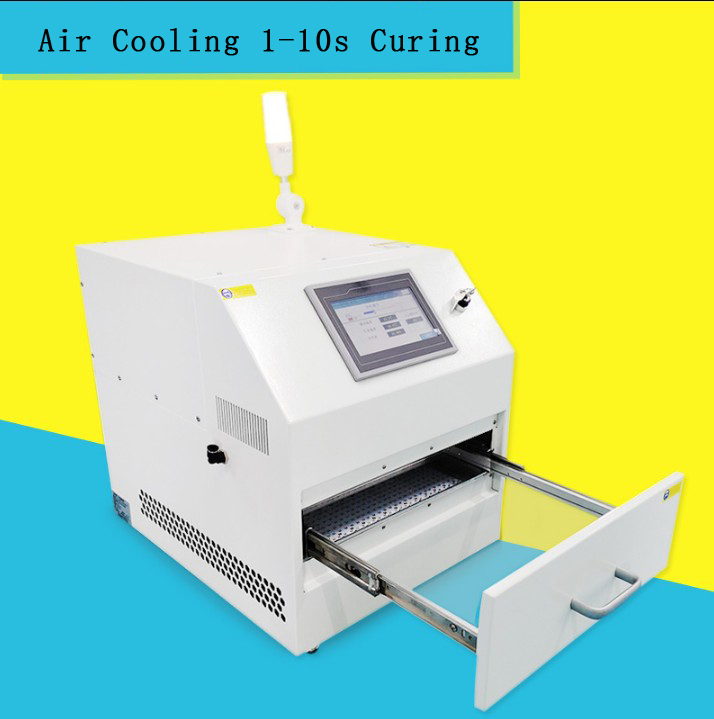